hamptonhills
Recruit
- Joined
- Sep 24, 2012
- Messages
- 2
I recently had to remove my 4" exhaust manifolds and elbows on my 2000 merc 5.7 engine in order to get to the oil pan to fix an oil pan leak. The manifolds are six years old so they were candidates for replacing. The internals looked acceptable but the the manifold/elbow joint (the weak link of the design) did not. I wanted to replace them with aluminum manifolds/elbows but they were not immediately available and I needed the boat back in the water ASAP so I needed a way to test that the manifolds and elbows would not leak.
I searched the the iboats forums and saw the acetone method of testing for leaks but this method tested only the manifold. I wanted to test the manifold and elbow together as one assembled unit. This requires that the exhaust and water portions of the manifold/elbow be completely isolated. After "kicking it around a little", it turned out to be easier and cheaper then I thought. I'm a long time iboats forum viewer, but a first time poster so I hope someone finds this post useful.
Testing Method Overview
In order to isolate the exhaust and water sides of the manifold/elbows you first have to plug the center exhaust hole in the elbow. This hole has a diameter of approximately 2 1/8"-2 1/4" which turns out to be very close to the size of a 2" PVC sewage pipe.
Since the exhaust elbow opening is at a slight angle, a 2" expandable PVC pipe plug will not seal off the the exhaust hole. In order to increase the diameter of the plug, you need to wrap it with some 1/2" self fusing silicone tape.
The plug will now seal off the center exhaust port.
Now lay the manifold/riser/elbow flat on its back so the the block exhaust manifold ports are pointing up and fill the exhaust ports with water and verify that no water is leaking out of the plugged center exhaust hole in the elbow.
You now have to plug the water side of the elbow. I did this my cutting a 3/4" piece of scrap plastic to plug the rubber exhaust sleeve.
I had to plug the Y pipe portion of the rubber sleeve due to elbow center exhaust clearance issues. You now apply air pressure to the water inlet port on the bottom of the manifold
if you don't see any bubbles coming from the water in the exhaust manifold ports or any hissing of escaping air your setup is sound.
Testing Method Detail
Items required
Step by Step Instructions
This post is specifically for 4" mercruiser 5.7 exhaust manifold/elbows but it should be easy to adapt for other applications.
I searched the the iboats forums and saw the acetone method of testing for leaks but this method tested only the manifold. I wanted to test the manifold and elbow together as one assembled unit. This requires that the exhaust and water portions of the manifold/elbow be completely isolated. After "kicking it around a little", it turned out to be easier and cheaper then I thought. I'm a long time iboats forum viewer, but a first time poster so I hope someone finds this post useful.
Testing Method Overview
In order to isolate the exhaust and water sides of the manifold/elbows you first have to plug the center exhaust hole in the elbow. This hole has a diameter of approximately 2 1/8"-2 1/4" which turns out to be very close to the size of a 2" PVC sewage pipe.
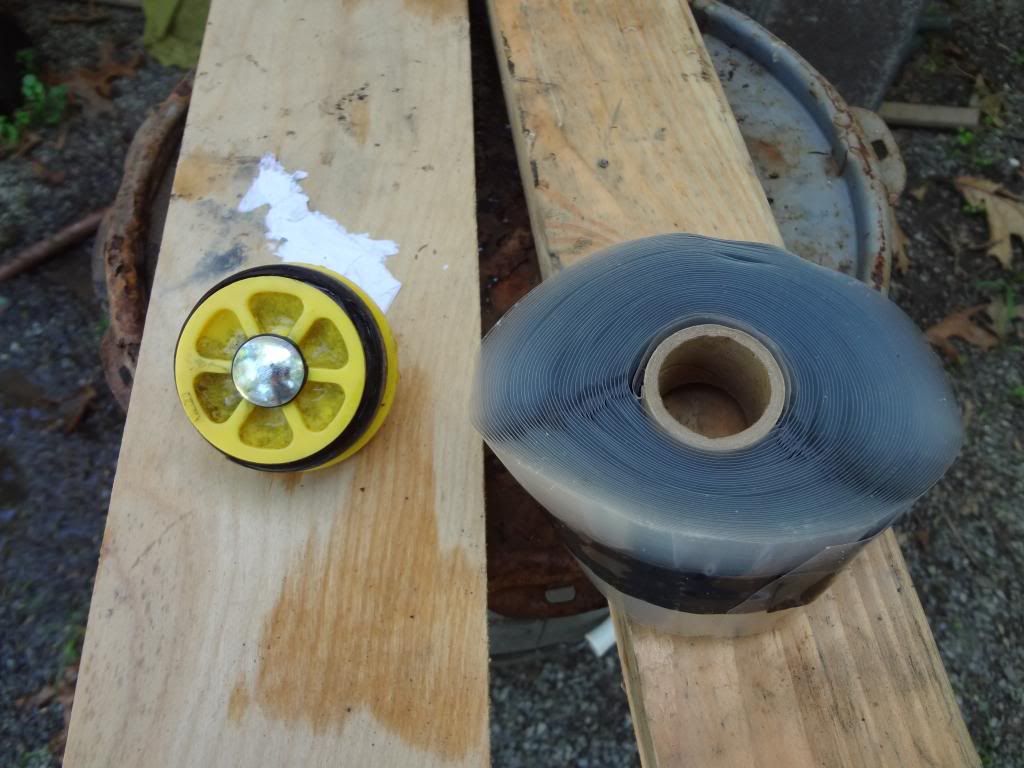
Since the exhaust elbow opening is at a slight angle, a 2" expandable PVC pipe plug will not seal off the the exhaust hole. In order to increase the diameter of the plug, you need to wrap it with some 1/2" self fusing silicone tape.
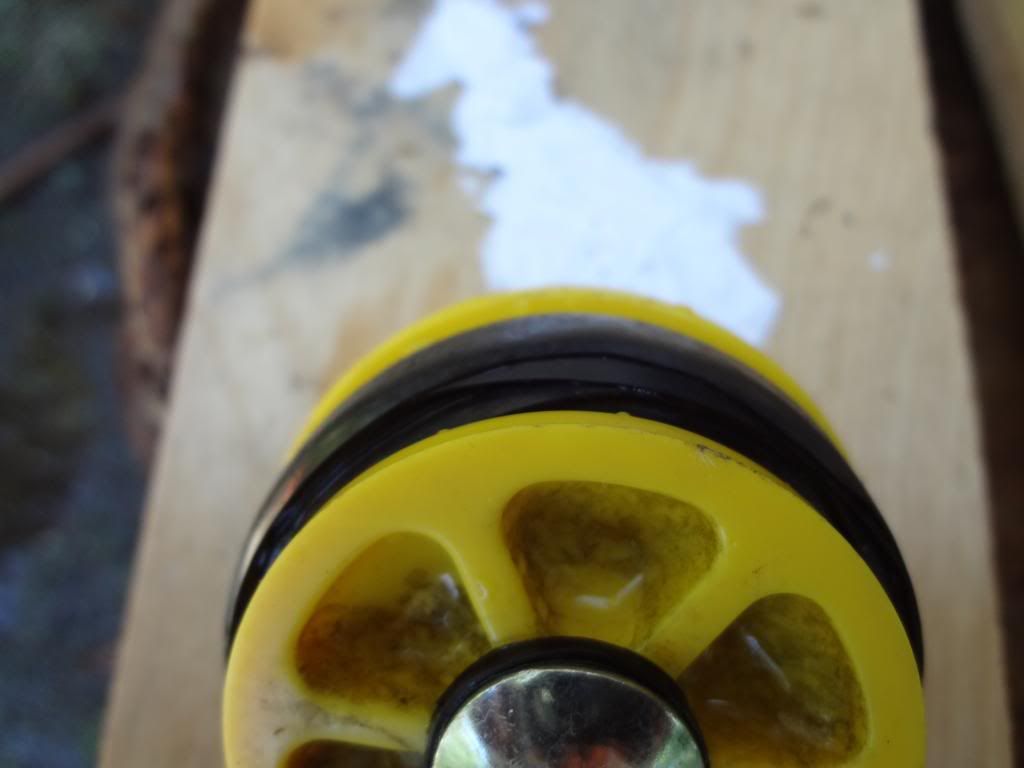
The plug will now seal off the center exhaust port.
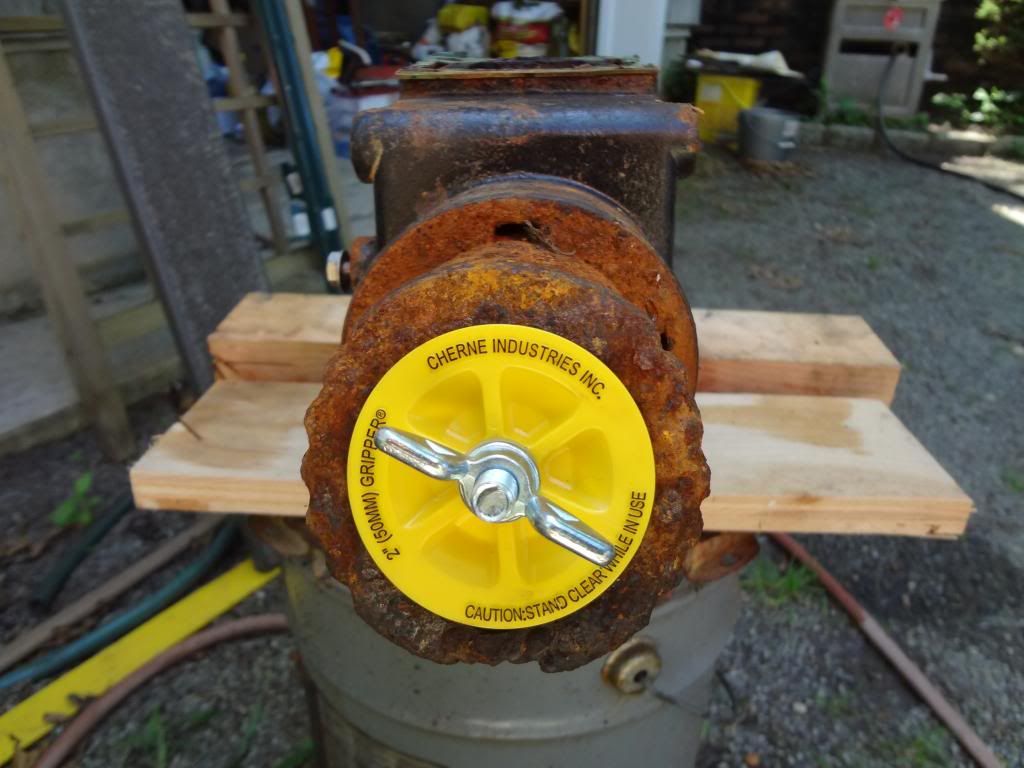
Now lay the manifold/riser/elbow flat on its back so the the block exhaust manifold ports are pointing up and fill the exhaust ports with water and verify that no water is leaking out of the plugged center exhaust hole in the elbow.
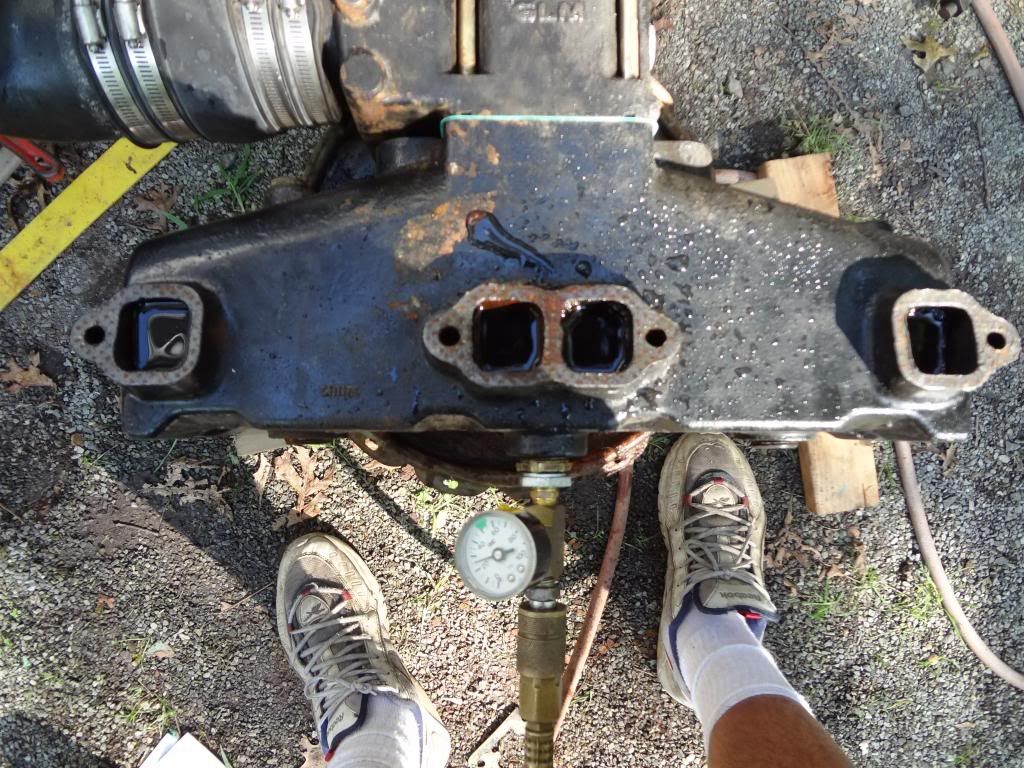
You now have to plug the water side of the elbow. I did this my cutting a 3/4" piece of scrap plastic to plug the rubber exhaust sleeve.
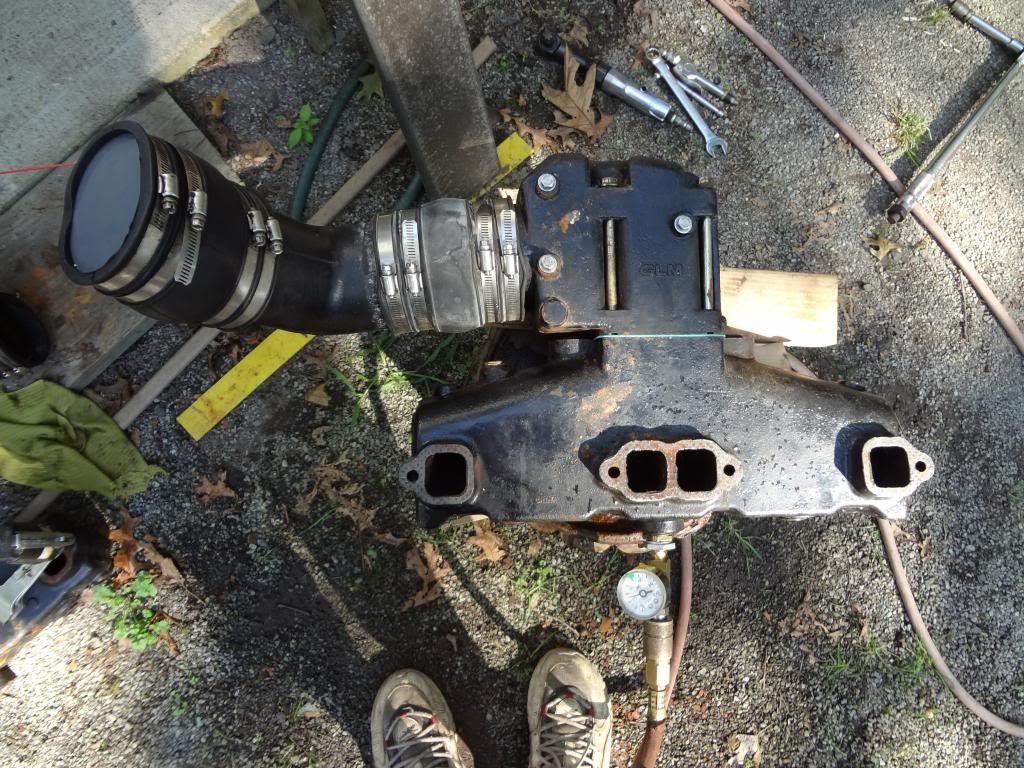
I had to plug the Y pipe portion of the rubber sleeve due to elbow center exhaust clearance issues. You now apply air pressure to the water inlet port on the bottom of the manifold
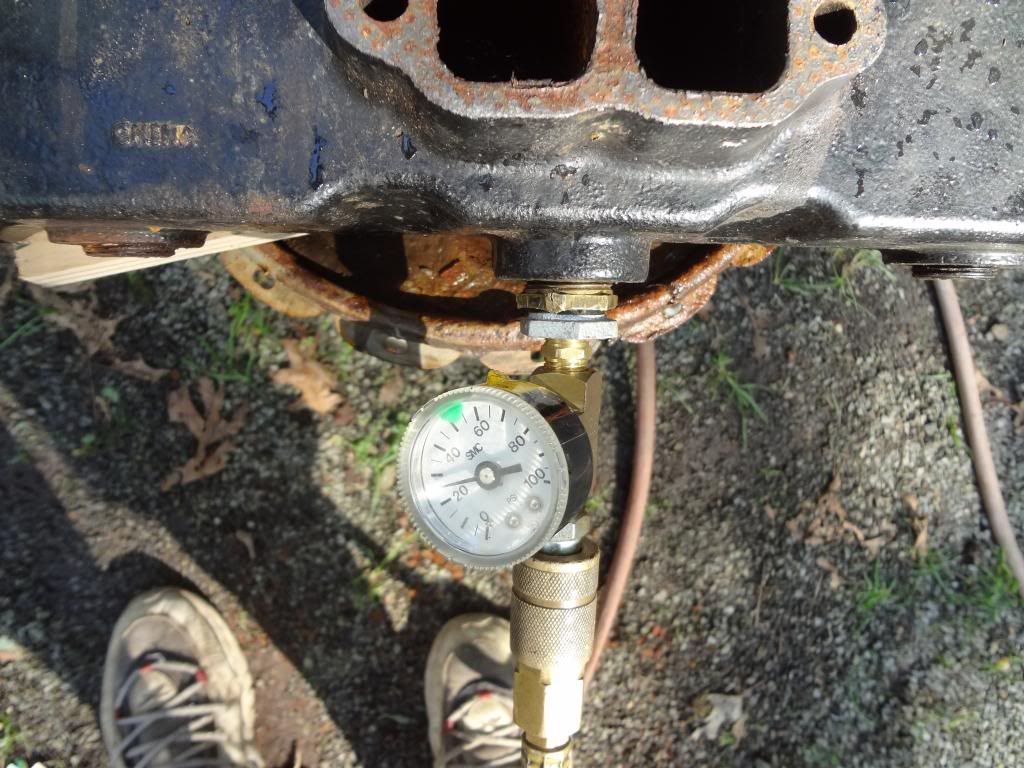
if you don't see any bubbles coming from the water in the exhaust manifold ports or any hissing of escaping air your setup is sound.
Testing Method Detail
Items required
- Expandable 2" PVC sewage pipe plug (Several dollars at your local plumbing supply store)
- Several feet of 1/2" self fusing silicone tape.
- 3/4" NPT to 1/4" NPT bushing if connecting directly to the manifold or a rubber hose and barb adapter.
- 1/4" NPT pressure gauge.
- 1/4" NPT Tee.
- 1/4" NPT valve.
- 1/4" NPT close nipple.
- 1/4" NPT air nipple.
- Water rubber sleeve plug (You have to make this yourself).
Step by Step Instructions
- Smooth out the inside of the output side of the exhaust hole in the elbow so that the 2" PVC plug will be able to "seat" nicely. I used a 1/4" straight carbide de-burring tool in a high speed grinder to accomplish this. It doesn't have to be perfect. You can verify the seal when you fill the manifold with water.
- Add the 1/2" self fusing silicone tape around the rubber gasket on the PVC plug in order to increase it's diameter. When using self fusing silicone tape you usually stretch the tape at least 50% in order to get the tape to fuse to itself better. With this application you want to use the stretch of the tape to plug the hole as the plug is expanded so you want minimize the stretch applied when the tape is installed. I used maybe a 20% stretch when applying the tape. Test the fit in the exhaust elbow.
- Install the PVC plug and tighten it down. I used a wrench so ensure it didn't leak.
- Fill the exhaust ports of the manifold with water. Make sure that the exhaust ports are the highest point on the unit. Tilt the manifold/elbow unit in order to make sure there is not trapped air in the unit.
- Verify that no is water leaking from the elbow center exhaust PVC plug.
- Create a water rubber sleeve plug. I used some scrap 3/4" plastic, a scroll saw, and belt sander. It doesn't have to be perfect since the sleeve is rubber and will conform to the plug. 2" wood should also work but I haven't tried it.
- Install the rubber exhaust sleeve and plug on the exhaust elbow.
- Create the air pressure delivery apparatus.
- Attach the air pressure delivery apparatus to the bottom of the exhaust manifold port.
- Pressurize the exhaust manifold water jacket. Since the pressurized system includes the rubber sleeves, be careful not to over pressure the manifold. I went a high as 25 PSI and you can see the rubber sleeves bulging. If you have an old set of rubber sleeves it might be a good idea to use them so you don't put undo stress on your operational sleeves.
- If you hear hissing coming from the rubber sleeves or the sleeve plug just tighten them until the hissing stops.
- Now look for any bubbles in the exhaust ports. If you don't see any bubbles after 15 mins you're setup is sound. You can also close the air valve and see if the pressure decreases over time, but when I was testing I could see also immediately whether there was a leak or not.
This post is specifically for 4" mercruiser 5.7 exhaust manifold/elbows but it should be easy to adapt for other applications.